Special promotions are available! Don't miss out on great deals!
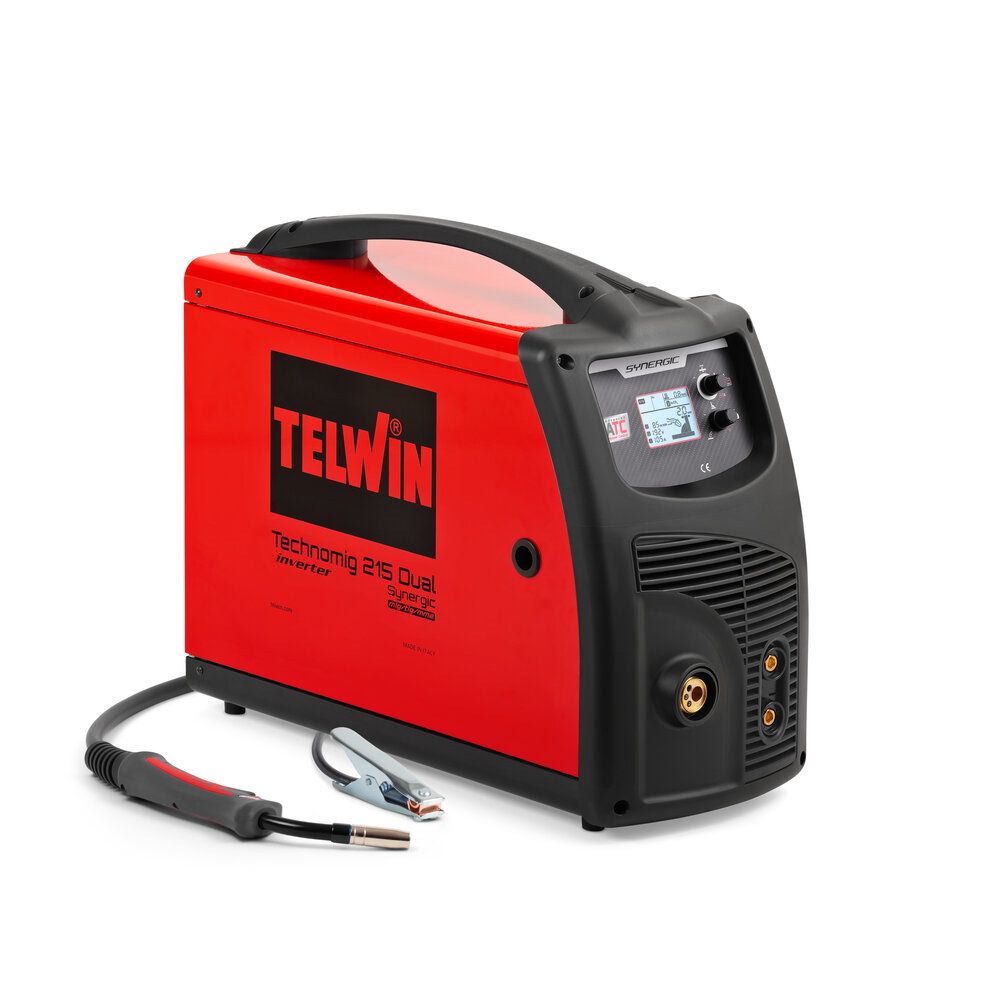
MIG-MAG/FLUX/BRAZING/MMA/TIG DC-Lift Technomig 215 Dual Synergic welder
Product code: 816232
Brand: Telwin
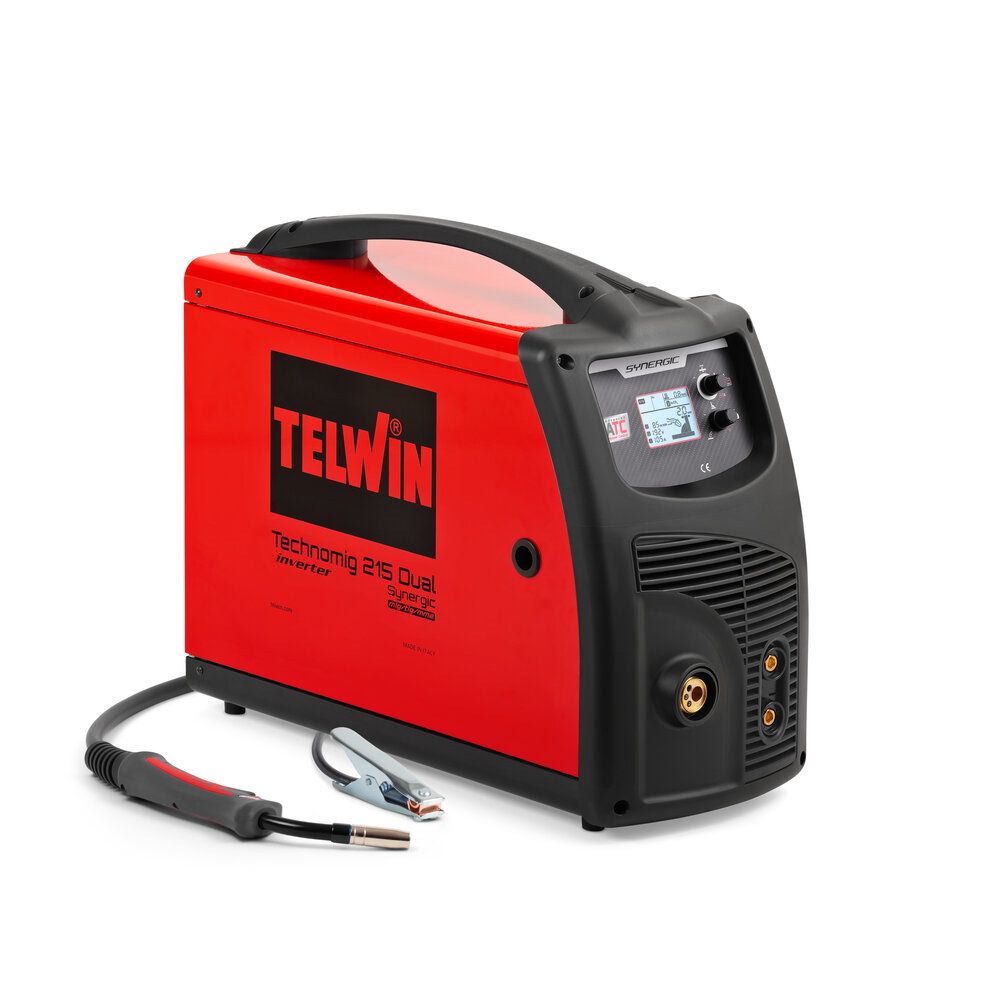
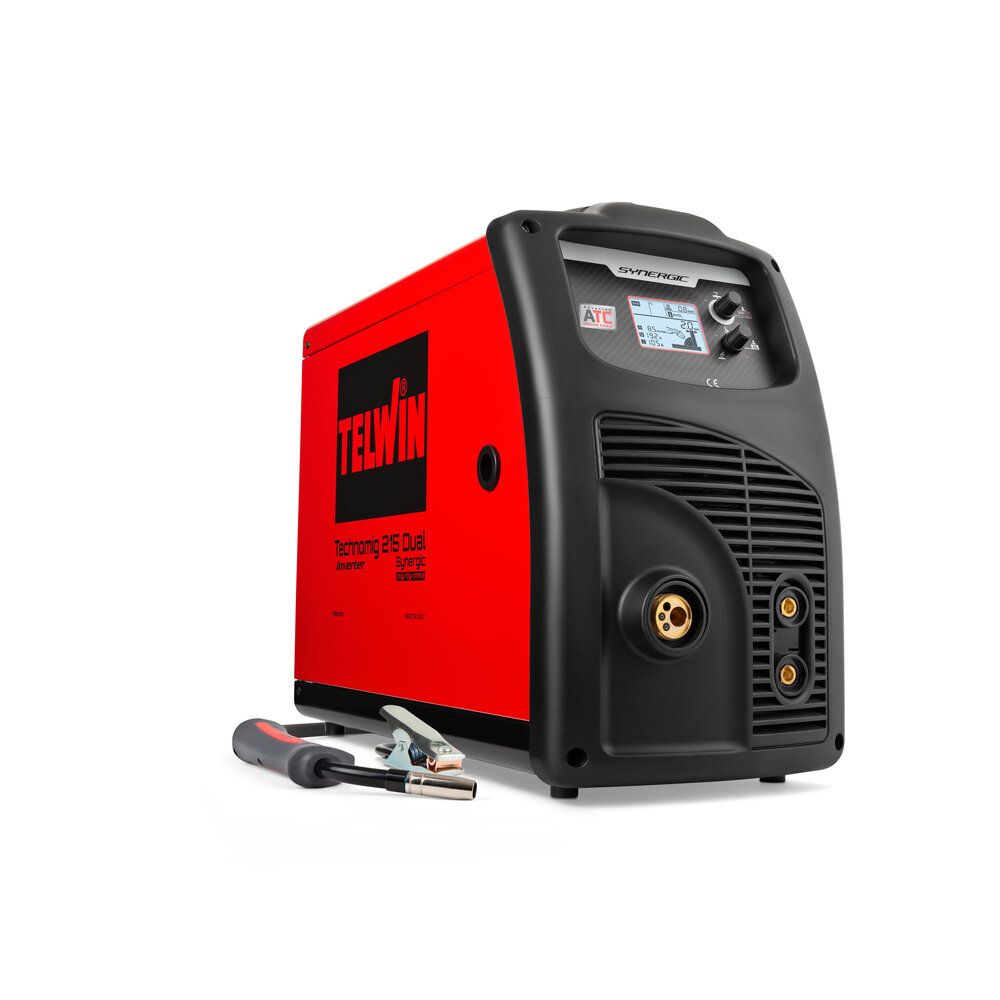

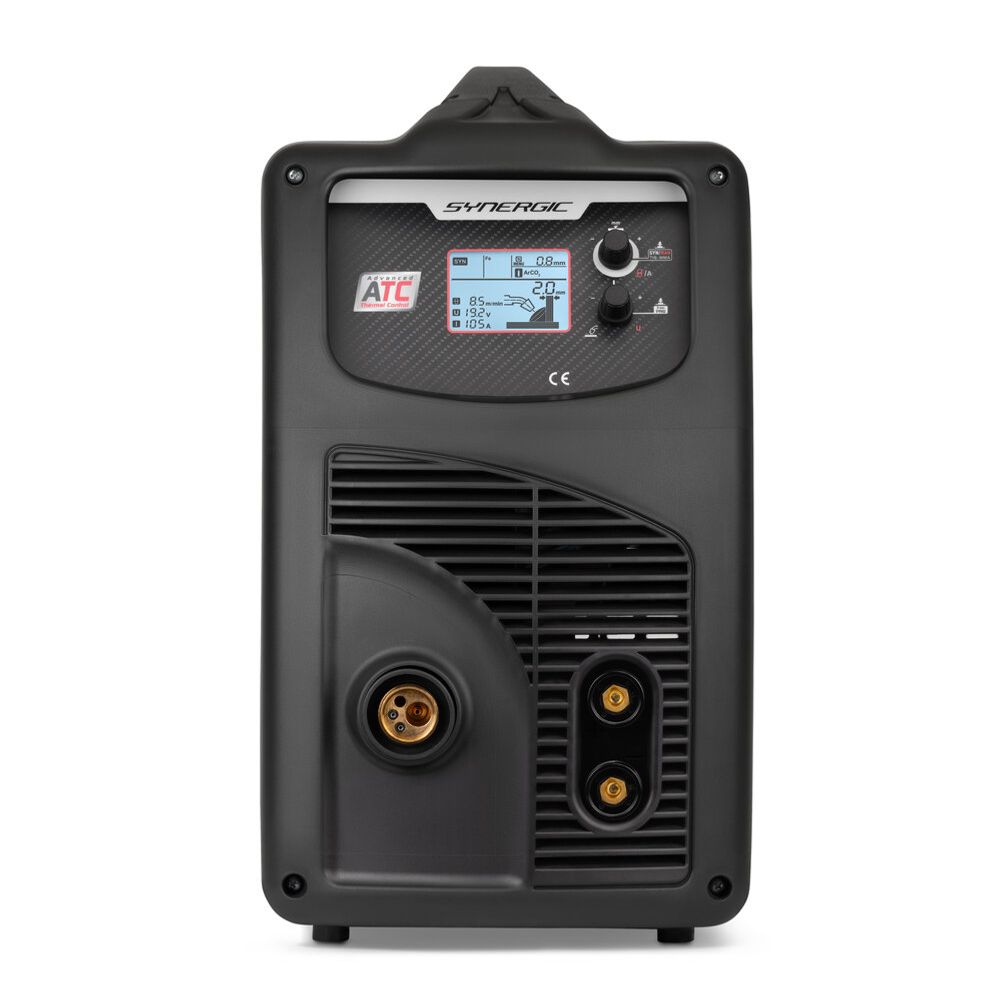
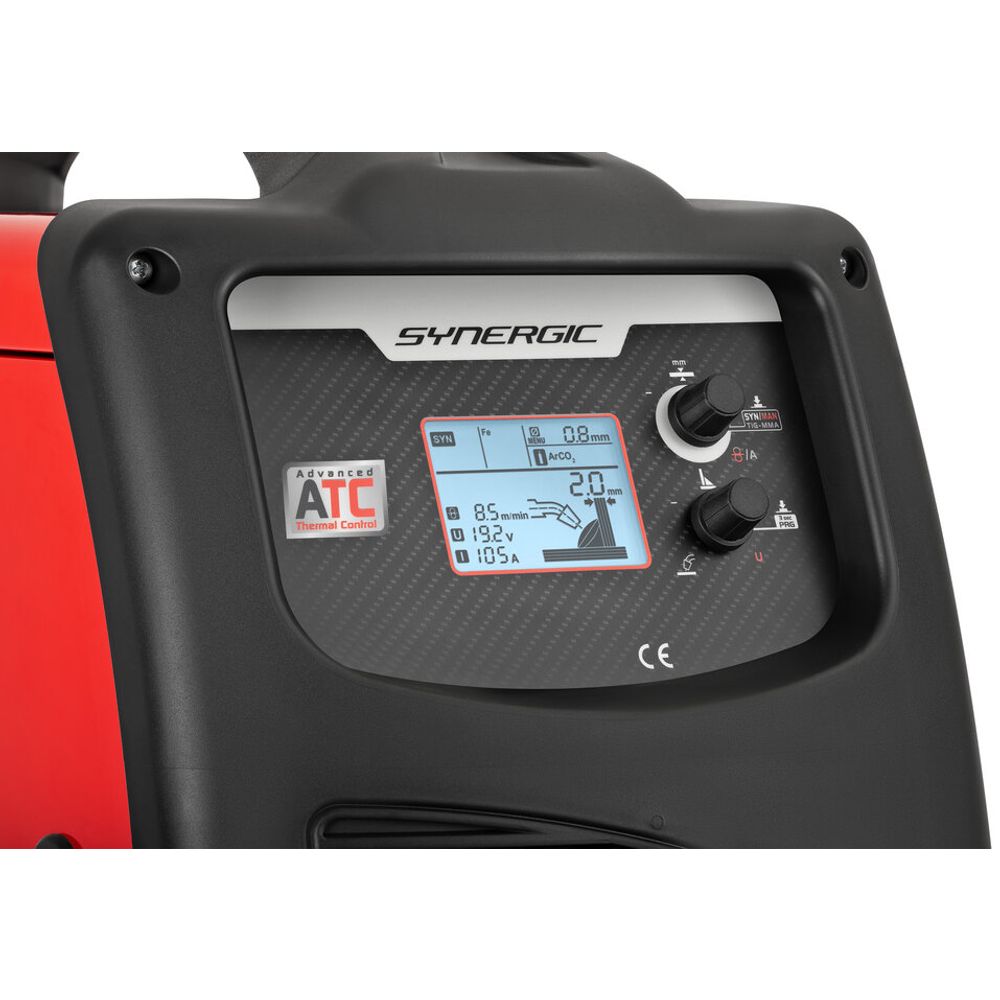
Product description
- This welding machine is a 220A source of current for arc welding, made specifically for MAG welding carbon steel or weak alloys with CO2 protective gas or Argon/CO2 mixes, using tubular full or core electrode wires. It is also ideal for MIG welding stainless steel with Argon gas containing + 1-2% oxygen and aluminium and CuSi3, CuAl8 (brazing) with Argon gas, using electrode wires that are suitable for the workpiece to be welded.
- Suitable core wires can be used without Flux protection gas, adapting torch polarity according to the indications of the wire producer. It is particularly suitable for light metalwork fabrication and in body shops, for welding galvanized plates, high stress stainless steel and aluminium.
- SYNERGIC operation ensures fast and easy welding parameter setting, always guaranteeing high arc control and welding quality (OneTouch Technology).
- The welding machine, where available, can be used for TIG welding in direct current (DC), with arc striking upon contact (LIFT ARC mode). It welds all types of steel (carbon, low- and high-alloy) and heavy metals (copper, nickel, titanium and their alloys) with a gas shield of pure (99.9%) Ar or, for special uses, with an Argon/Helium mix.
- It can also be used for MMA electrode welding in direct current (DC) using coated electrodes (rutile, acid, basic).
- Microprocessor controlled MIG-MAG/FLUX/BRAZING/MMA/TIG DC-Lift inverter multiprocess welding machine.
- Technomig 215 Dual Synergic is confirmed as the perfect solution for a wide range of applications, from maintenance to installation and interventions in body shops, because of its flexibility and the different materials it can weld (steel, stainless steel, aluminium) or braze weld (galvanized sheet).
- Thanks to ONE TOUCH LCD SYNERGY technology, fast synergic control of welding parameters makes the product easy to use. Intelligent and automatic control of the arc moment by moment maintains high welding performance under all working conditions, with different materials and/or gases. Just set the material thickness and start welding. 27 preset synergic curves. These curves are effectively predefined welding programs that automatically control the welding parameters according to the selected job. The welder just needs to select the right curve for the welding job and the machine automatically sets the most appropriate voltage and wire feed speed, ensuring the best possible weld quality and efficiency.
- 27 synergy curves available.
- Max. spool 15kg, 200 and 300mm
- ATC (Advanced Thermal Control) to facilitate welding on thin materials.
- MMA: Advanced arc control devices: arc force, hot start, anti-stick.
- Lightweight and very compact, Technomig can be moved around easily in all intervention areas, both indoors and outdoors.
- Polarity reversal for NO GAS/Flux, MIG-MAG/BRAZING welding.
- Visualization on LCD display of voltage, current, welding speed.
- Regulation of: wire speed up slope, electronic reactance, burn-back time, post gas.
- Choice of 2/4 times, spot operation.
- VRD device: Improves safety during welding operations. The VRD (Voltage Reduction Device) function allows to decrease the output voltage, increasing the operator’s safety when working in humid or particularly dusty environments.
- Thermostatic, overvoltage, undervoltage, overcurrent, motorgenerator (+/- 15%) protections.
- Complete with MIG-MAG torch (MT15, 3m), work clamp and cable.
The ATC (Advanced Thermal Control) technology
The Made in Telwin ATC technology is designed for use in specific sectors such as, for example, car bodywork where the materials (with thin materials measuring from 0.5-0.8 mm) are extremely sensitive to deformation caused by the temperatures reached during welding operations.
The ATC technology makes it easy to achieve excellent standards of welding on thin materials thanks to state-of-the-art control of the arc.
Advantages
- Easy welding of thin materials
- Decreased deformation of material
- Extremely stable arc even whenworking with low currents
- Rapid and accurate tack welding
- Easier coupling of spaced sheets
- Excellent results on steel, aluminium and during brazing operations
MIG-MAG
- Synergic (automatic) or manual operation
- Pre-set synergic curves
- Wire speed, welding voltage and welding current shown on an LCD screen
- 2T, 4T and spot operation selection
2T: Welding begins when the torch push-button is pressed and ends when the push-button is released.
4T: Welding begins when the torch push-button is pressed and released, and ends only when the torch push-button is pressed and released a second time. This mode is useful for long welding operations.
Spot: Used for MIG/MAG spot welding with control of welding duration.
- Adjustments: wire up slope, electronic reactance, wire burn-back time, post gas
Electronic reactance: Adjusting the reactance during MIG/MAG welding allows you to fine-tune the inductance of the welding circuit. By adjusting the reactance, the welder can optimize the behavior of the welding arc when welding different material thicknesses and types, improving the quality of welding and facilitating the welding process. Settings from - 10 % (low reactance machines) to + 10 % (high reactance machines). Factory value: 0 %.
Wire upslope: This setting allows you to gradually increase the speed of the welding wire at the beginning of welding. This helps reduce welding errors such as excessive penetration or spatter when the arc is struck, ensuring a smoother start and transition in the welding process. Settings from - 10 % to + 10 %. Factory value: 0 %.
Wire burnback time setting: This setting controls the amount of time the wire can "burn back" after welding is complete before it automatically stops. Setting the proper burnback time ensures that the wire does not burn back too short, making it easier to start the next welding cycle. Settings from - 10 % to + 10 %. Factory value: 0 %.
Post-gas setting: This function controls the amount of time that shielding gas continues to flow after welding is completed to protect the still-hot weld from airborne contaminants until it cools down. Settings from 0 to 10 seconds. Factory value: 1 sec.
Wire speed correction: It increases or decreases the wire feed speed according to the display. Adjustment from -3 to +3m/min. Factory value: 0 m/min.
- Polarity change for GAS MIG-MAG/BRAZING welding or NO GAS/FLUX
- Setting the metric or UK system
TIG
- Start LIFT: The electric arc is struck by moving the tungsten electrode away from the piece to be welded. This strike mode causes less electrical-radiation disturbance and reduces tungsten inclusions and electrode wear to a minimum.
- Wire speed and welding current shown on an LCD screen.
MMA
- Arc force: This helps maintain a stable arc even in difficult conditions, such as dense welds. With the Arc Force function, the inverter automatically adjusts the current depending on the length of the arc. If the arc accidentally touches the workpiece, the current increases, so it does not stick. If the two are too far apart, the current will be reduced and the arc will not extinguish.
- Hot start: It helps to ignite the arc more easily by automatically increasing the current at the beginning of the welding process. This can be especially useful for difficult-to-ignite electrodes. Facilitates arc ignition for materials that are too cold or too thick.
- Anti-stick: Prevents the electrode from sticking to the workpiece, reducing the current connected to the electrode when it detects sticking. This makes it easier to remove the electrode and reduces the risk of overheating.
- VRD device: Improves safety during welding operations. The VRD (Voltage Reduction Device) function allows to decrease the output voltage, increasing the operator’s safety when working in humid or particularly dusty environments.
- Indication of recommended electrode diameter based on welding current.
- Wire speed and welding current shown on an LCD screen.
PROTECTION
- Thermostatic safeguard: A heat-sensing system that shuts down the machine if the temperature rises too high, preventing overheating.
- Protection against accidental short-circuits caused by contact between torch and earth
- Protection against irregular voltage (power supply voltage too high or too low)
- Anti-stick (MMA).
STANDARD ACCESSORIES
- MIG-MAG torch (MT15, 3m)
- Return cable complete with earth clamp
Specifications
Single phase mains voltage: 230V | Mains frequency: 50/60Hz |
Current Range: 20-220A | Max Current: 180A@20% |
DC current: 100A | Max. no load voltage: 52V |
Max. absorbed current: 31A | Absorbed current at 60%: 15A |
Max. absorbed power: 5kW | Absorbed power at 60%: 2,2kW |
Efficiency: 85% | Power factor: 0,7 |
Usable electrodes in DC: 1,6-3,2mm | Steel welding wire diameter: 0,6-1mm |
Inox welding wire diameter: 0,8-1mm | Aluminium welding wire diameter: 0,8-1mm |
Flux cored welding wire diameter: 0,8-1,2mm | Brazing wire deameter: 0,8-1mm |
Protection degree: IP23 | Dimensions: 62 x 26 x 49cm |
Weight: 21,8kg |
Product packing
Pack number | Dimensions | Weight |
---|---|---|
1 | 71 x 30 x 56 cm | 23.7 kg |
Delivery fee
Delivery method | Gross price |
---|---|
Pickup in Nagytarcsa | 0,00 € |
Pickup in Debrecen | 0,00 € |
DHL Worldwide Express | 227,58 € |